Manufacturing Management
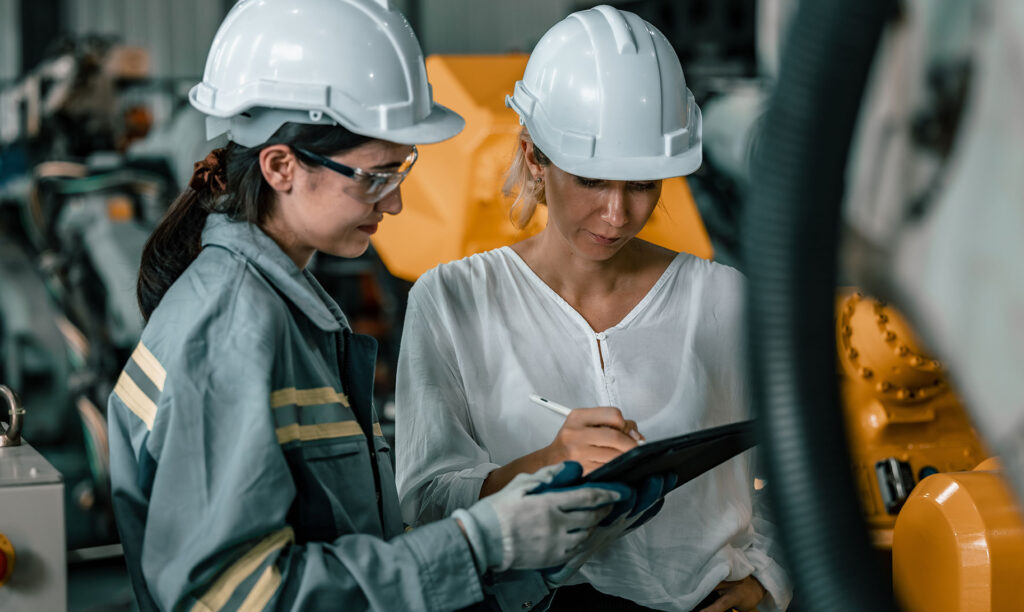
Assembly management
Specify a list of sellable the items, raw materials, sub-assemblies, and resources as an assembly bill of materials that make up a finished item or a kit. Use assembly orders to replenish assembly items. Capture customer requirements for the kit’s bill of materials directly from sales quotes, blanket orders, and order lines in the assembly-to-order processes
Standard cost worksheet
Give company controllers a reliable and efficient way to maintain accurate inventory costs. Work with standard cost updates in Business Central in the same way you would in an Excel spreadsheet. Prepare for cost updates without changing data until you’re ready.
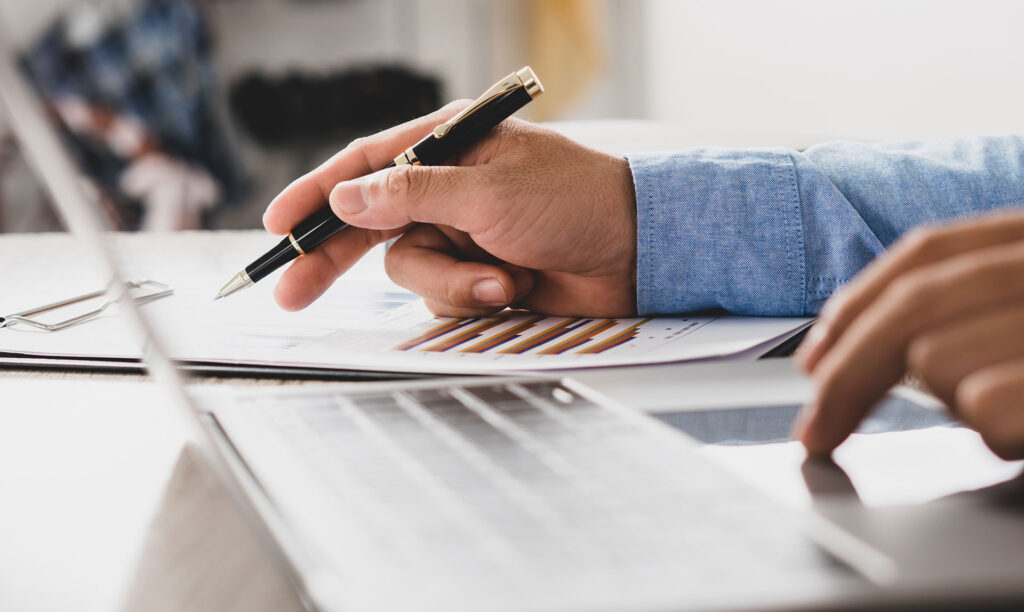
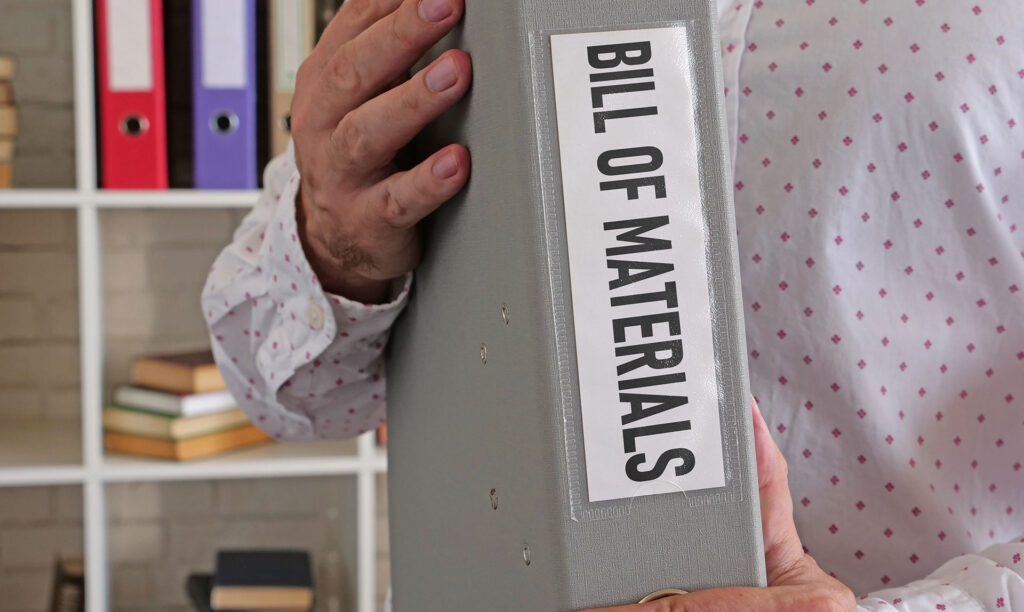
Product bill of materials
Create bills of materials and calculate their standard costs. Keep track of different versions and know which components were valid at a specific moment of time and for specific production batch.
Basic capacity planning
Add capacities (work centers) to the manufacturing process. Set up routings for production orders and material requirements planning. View loads and the task list for the capacities.
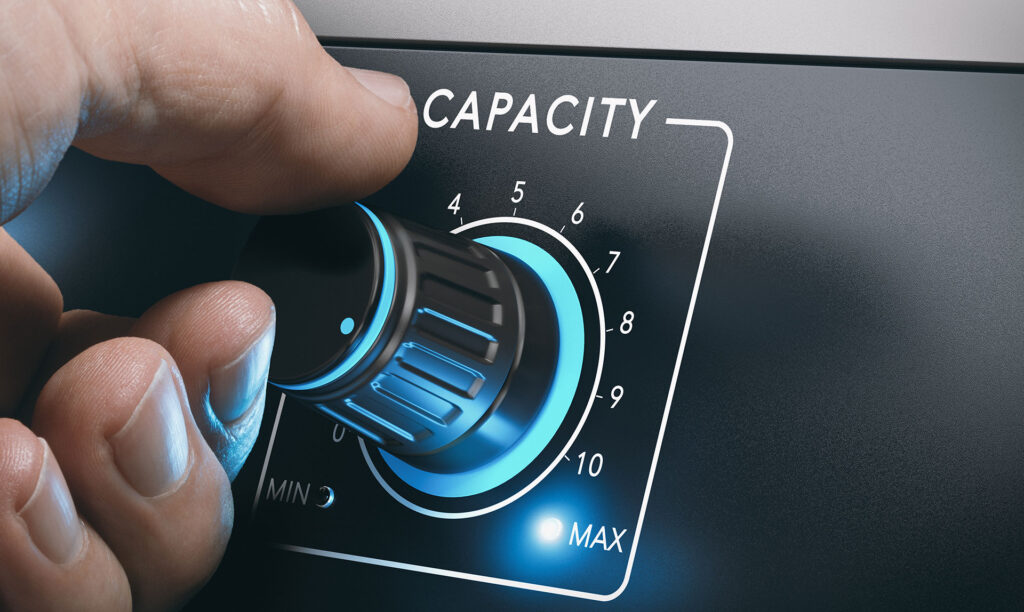
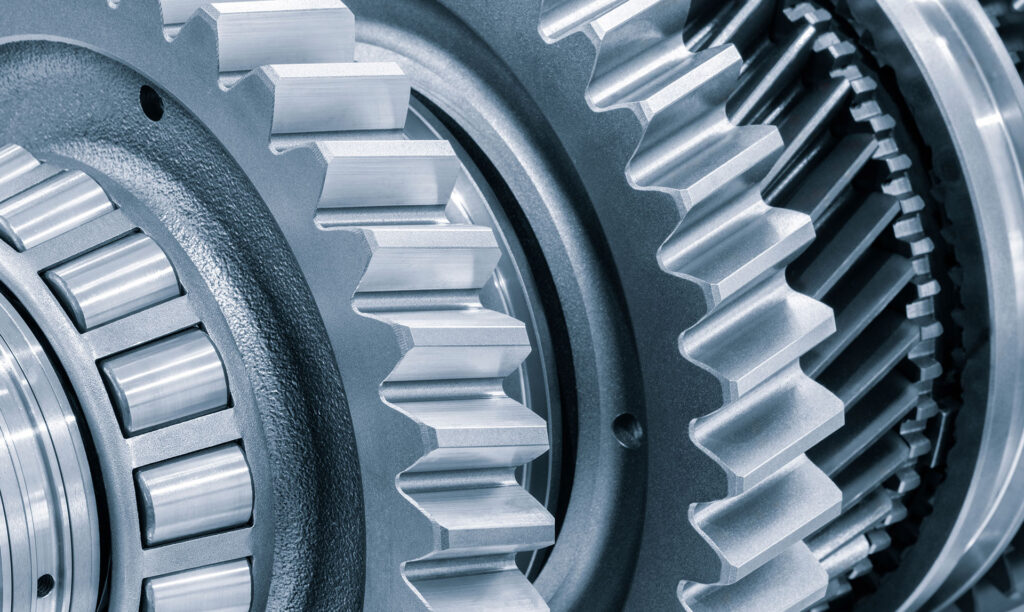
Machine Centers
Add machine centers as capacities in the manufacturing process. Manage capacity for each machine or production resource on a detailed level for machine centers, and on a consolidated level for work centers. Use machine centers to store default information about manufacturing processes, such as setup, wait, and move times and default scrap percentages.
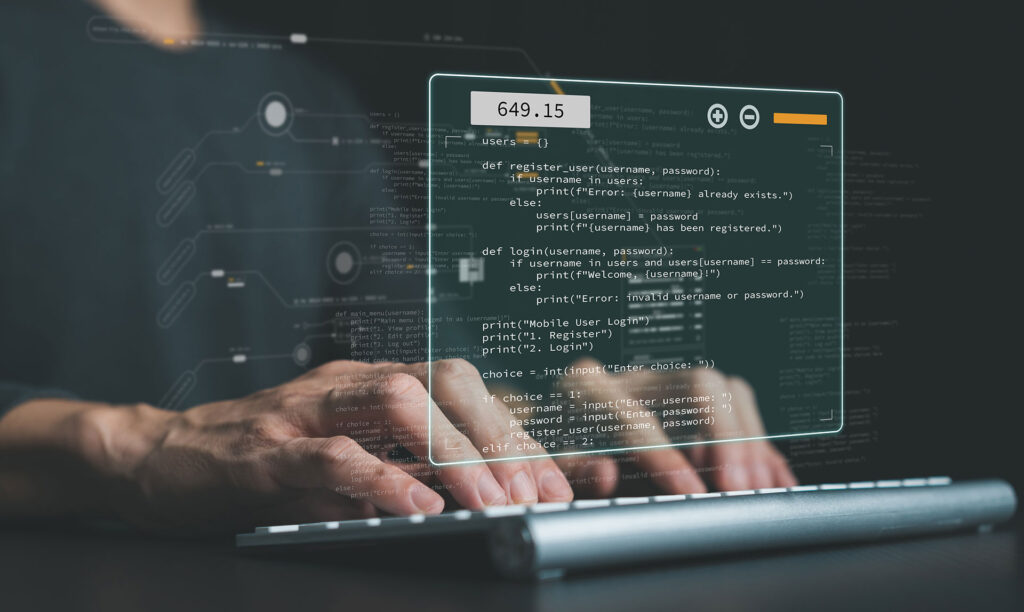
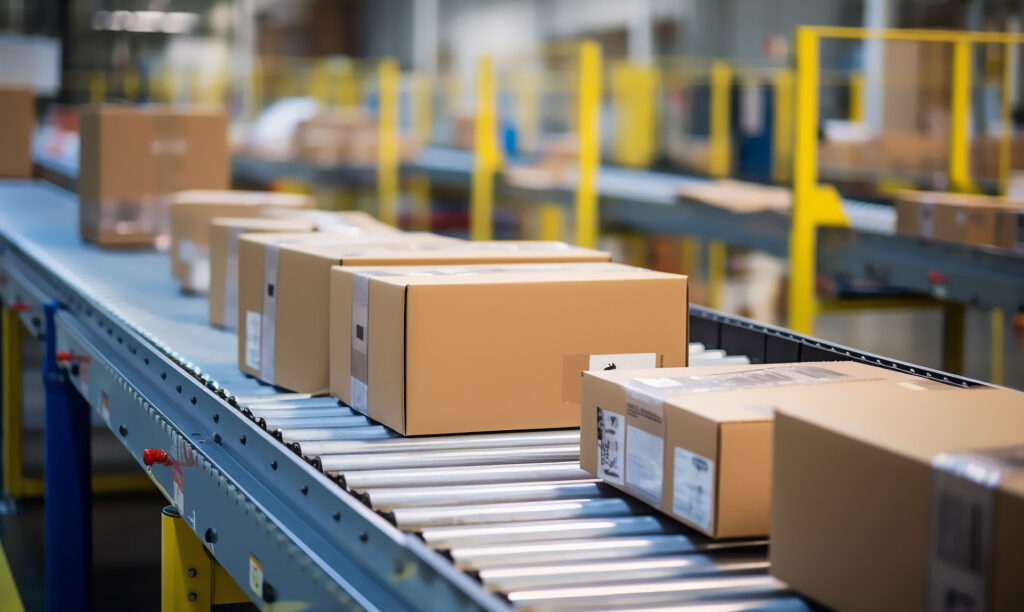
Production Orders
Create production orders and post consumption and output. Calculate net requirements based on production orders. Use a manual supply planning tool as an alternative to automatic planning. Get visibility and tools to manually plan for demand from sales lines and to create supply orders.
Automatic Components and Capacity Consumption
Reduce data entry, and have accurate stock and WIP information in the same time. Use routing codes to link components with specific operation to minimize waste by implementing just-in-time principles.
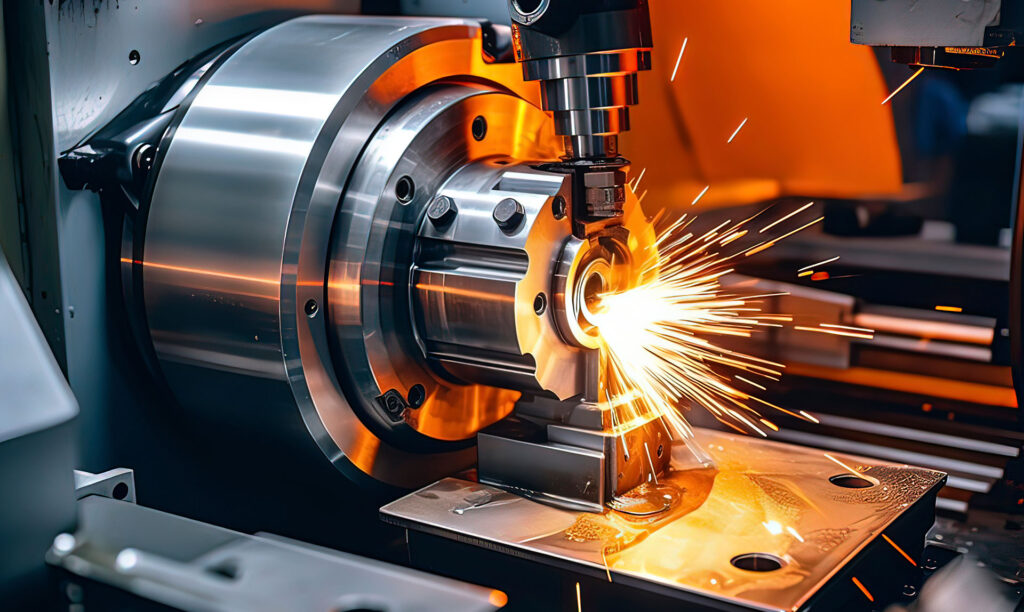
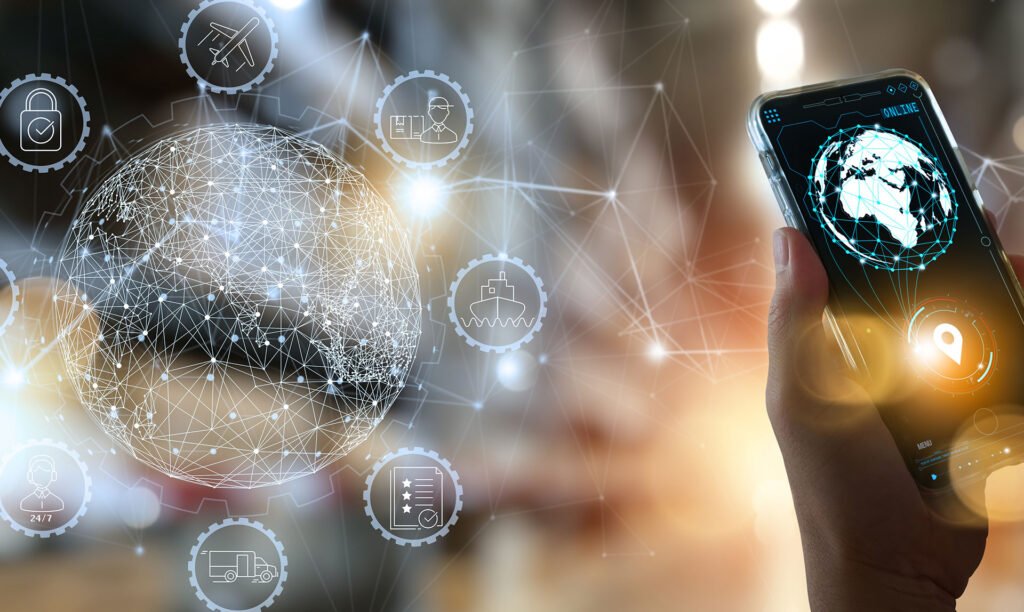
Subcontracting
Delegate all or part of operations to external work centers. Use separate location and transfer order to track raw materials. Register performed work with purchase orders.
Finite loading
Manage finite loading of capacity-constraint resources. Account for capacity constraints for periods to avoid overloading work centers.
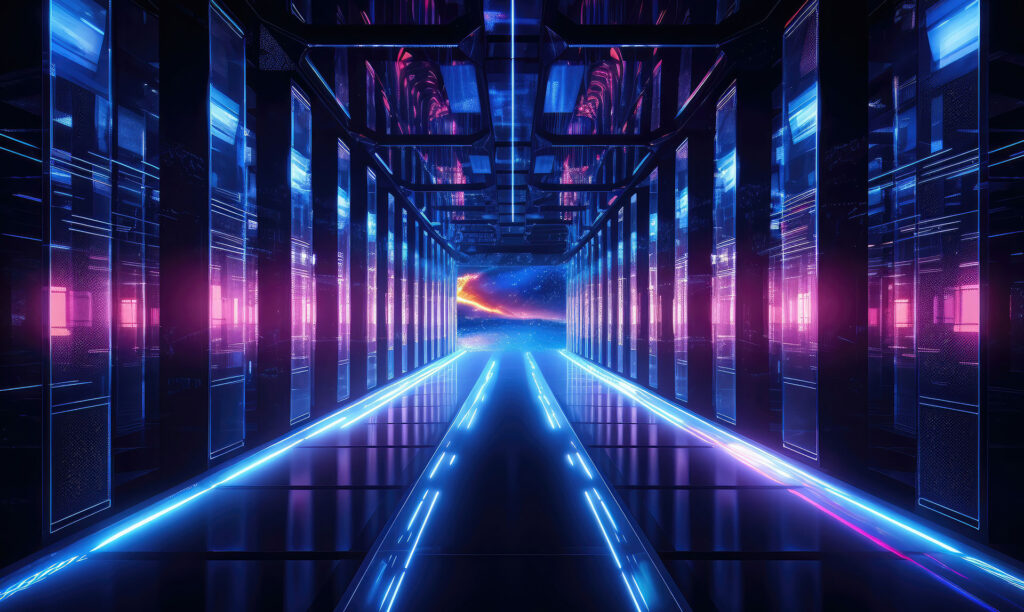
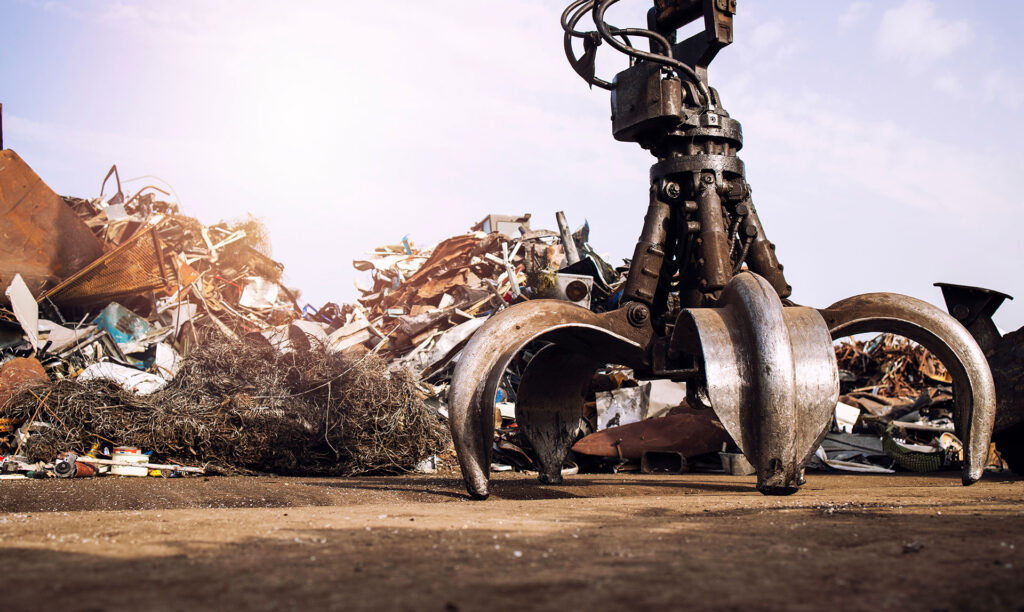
Scrap
Scrap can be inevitable in the manufacturing process. But making sure it is properly recorded is essential to proper inventory and cost management.